LVL Corner
The art and art of unwinding
The THEBAULT Group is celebrating its 70th anniversary this year. A special opportunity to look back at the Group's historic know-how in peeling with Benoît THEBAULT, who knows the subject particularly well.
The ancient origins of peeling
People have always been ingenious at working with wood. Peeling probably has its origins in marquetry skills, which the Egyptians were probably the first to master. The Egyptians were probably the first to master the technique, using a very sharp knife to remove thin layers of wood from various, generally noble, species to decorate furniture. Marquetry reached its golden age with the great Italian and then French cabinetmakers in the 17th and 18th centuries.
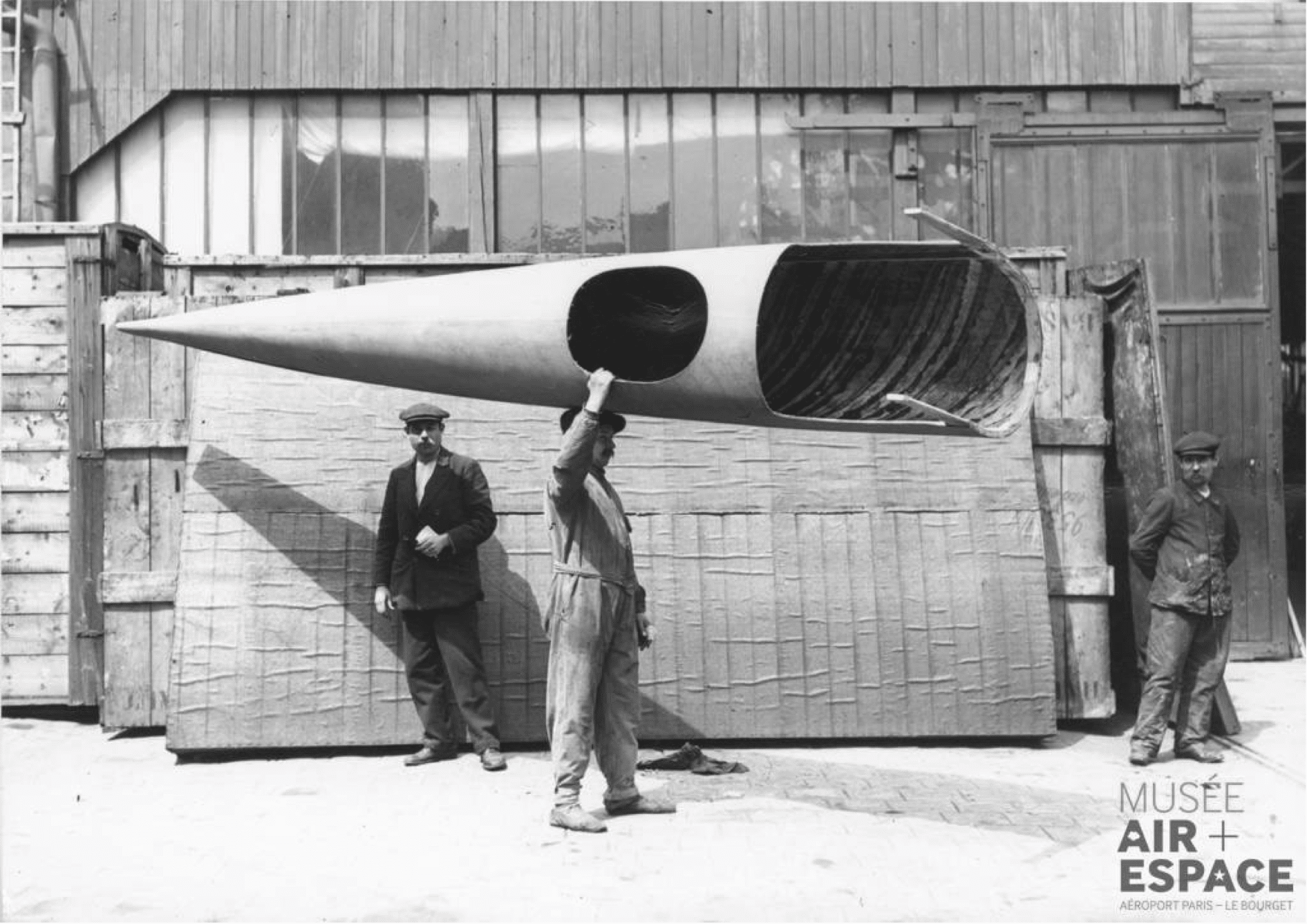
Peeling in the industrial age
The Industrial Revolution saw the technical evolution of know-how in the world of wood. As early as the middle of the 19th century, patents for peeling processes were registered in Europe. The first patent for peeled plywood was registered in 1883, and the first factory was built in Czechoslovakia. In France, the first machine manufacturers set up shop. Poplar peeling in particular was in vogue to supply the packaging industry. It was in the United States, with its abundant softwood resources, that peeled plywood entered a phase of large-scale production. In Europe, with the outbreak of the First World War, the manufacture of structured wood expanded rapidly to meet the needs of the burgeoning aeronautics industry and munitions packaging.
Modern peeling
In the 1960s, a French machine from 1926 was still in operation in the THEBAULT workshops, illustrating the industrial reality of peeling in France after the First World War. This Valette & Garreau machine was already technically advanced. The company disappeared, overtaken by Italian competitors.
Production techniques evolved considerably in the 80s, with the widespread use of hydraulics and, above all, electronics, the precursors of numerical control. Improvements in wood centering techniques significantly boosted yields.
The human touch
Technology isn't everything. When it comes to peeling, the machine operator's know-how is essential, the fruit of many years of practical experience.
There are many criteria to be taken into account by the operator: species, origin, steaming, etc. The operator also checks quality visually.
Exotic logs are generally peeled more slowly. They are peeled in several thicknesses to produce the finest veneers for use on the panel faces. Softwood logs are peeled more quickly in a single layer, requiring more attention from the operator, who must also anticipate the peeling of the next log.
Unwinding phases
The production site receives whole logs, which are debarked and then cut to size. They are then put into ovens at 60 degrees for 24 hours to soften the material, particularly the hard knots, and remove some of the resin. Poplar and okoumé do not undergo the steaming stage.
The logs are then taken to the production line for peeling. The resulting veneers are cut to the desired size, then graded and stacked according to their moisture content.
Post-release operations
On leaving the kiln, at less than 3% moisture content, all sheets are re-sorted by density and visual appearance, then classified into 10 different grades. The best quality veneers are used for the outer faces of the panel, while the others are used for the inner faces. The curvature of the sheets is cancelled by opposing the veneers to balance and stabilize the panel. The panel is glued, cold-pressed and then hot-pressed. It is then cut and stored for shipment.
Pectin fir peeling for TEBOLVL has its own special features. The machine can handle very large-diameter logs, up to 900 mm. At the end of the drying process, the density criterion is taken into account to obtain the required mechanical strength.
The future of decoiling
It is generally accepted that the peeling technique is now technologically mature, although there is still room for improvement. Machine manufacturers are currently working to minimize the size of the peeling core by reducing its diameter from 8 cm to 2.5 cm. This highlights the imperative for our industry to maximize the use of material, which is more precious than ever.