Ressources
LVL Corner
L’art et la manière de dérouler
Le Groupe THEBAULT célèbre cette année ces 70 ans d’existence. Une occasion privilégiée de revenir sur le savoir-faire historique du Groupe en matière de déroulage avec Benoît THEBAULT qui connaît particulièrement bien le sujet.
L’origine lointaine du déroulage
De tous temps, les hommes se sont ingéniés à travailler le bois. Le déroulage trouve probablement son origine dans le savoir-faire en marqueterie dont les Égyptiens furent vraisemblablement les premiers à maîtriser la technique. Il s’agissait de prélever avec un couteau très tranchant de fines épaisseurs de bois de diverses essences généralement nobles pour décorer le mobilier. La marqueterie connaitra son âge d’or avec les grands ébénistes italiens puis français au XVII et XVIIIème siècle.
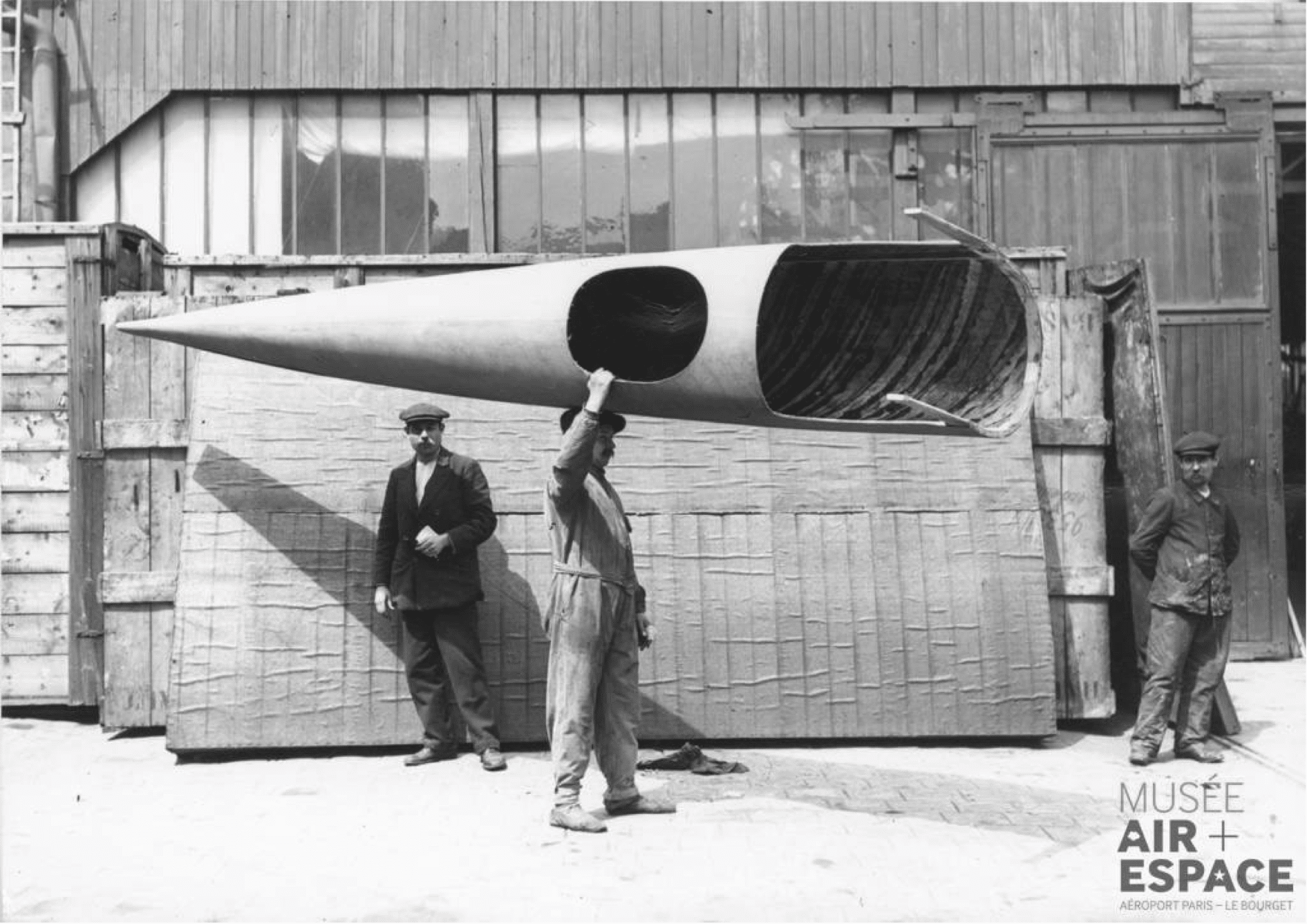
Le déroulage à l’ère industrielle
La révolution industrielle voit évoluer techniquement les savoir-faire dans l’univers du bois. Dès le milieu du XIXème siècle, des brevets de procédé de déroulage sont déposés en Europe. Le premier brevet de contreplaqué obtenu par déroulage est déposé en 1883 et une première usine voit le jour en Tchécoslovaquie. En France, les premiers fabricants de machine s’implantent. Le déroulage du peuplier notamment était en vogue pour fournir les industriels de l’emballage. C’est aux États-Unis qui dispose alors d’une ressource abondante en bois résineux que le contreplaqué par déroulage entre dans une phase de production à grande échelle. En Europe, avec la première guerre mondiale, la fabrication de bois structurés se développe fortement pour répondre aux besoins de l’industrie aéronautique naissante et le conditionnement des munitions.
Le déroulage moderne
Dans les années soixante, une machine française de 1926 était toujours opérationnelle dans les ateliers THEBAULT ce qui illustre la réalité industrielle du déroulage en France après le premier conflit mondial. Cette machine de la marque Valette & Garreau était déjà très aboutie sur le plan technique. La société disparaitra rattrapée par la concurrence italienne.
Les techniques de production évolueront fortement dans les années 80 avec la généralisation de l’hydraulique et surtout de l’électronique, prémices de la commande numérique. L’amélioration de la technique de centrage du bois a permis d’améliorer sensiblement les rendements.
L’humain garde la main
La technologie ne fait pas tout. En matière de déroulage, le savoir-faire du conducteur de la machine est essentiel, fruit de nombreuses années de pratique.
Les critères à prendre en compte par l’opérateur sont multiples : nature de l’essence, provenance, étuvage… L’opérateur contrôle également visuellement la qualité.
Les grumes de bois exotiques sont généralement déroulées plus lentement. Elles sont déroulées en plusieurs épaisseurs pour produire les plus beaux placages qui seront utilisés sur les faces du panneau. Les grumes de résineux sont déroulées plus rapidement en une seule épaisseur ce qui requiert plus d’attention de la part de l’opérateur qui doit également anticiper le déroulage de la grume suivante.
Les phases du déroulage
Le site de production reçoit les grumes entières qui sont écorcées puis tronçonnées à dimension. Elles sont alors rentrées dans les étuves à 60 degrés pendant 24 heures afin de ramollir la matière notamment les nœuds durs et retirer une partie de la résine. Le peuplier et l’okoumé ne subissent pas l’étape de l’étuvage.
Les grumes sont alors amenées jusqu’à la chaine de production pour le déroulage. Les placages obtenus sont alors coupés au format désiré puis classés et empilés selon leur degré d’humidité.
Les opérations post-déroulage
En sortie de séchoir, à moins de 3% d’humidité, toutes les feuilles sont retriées par densité et par aspect visuelle puis classées en 10 qualités différentes. Les placages de meilleure qualité sont utilisés pour les faces extérieures du panneau et les autres en partie intérieure. Le galbe des feuilles est annulé en opposant les placages pour équilibrer et rendre le panneau stable. Le panneau est encollé puis pressé à froid suivi d’un pressage à chaud. Il est ensuite découpé et stocké en vue de son expédition.
Le déroulage de sapin pectiné pour fabriquer le TEBOLVL présente des spécificités. La machine peut accueillir des grumes de très grand diamètre, jusqu’à 900 mm. En sortie de séchage, le critère de densité est pris en compte pour obtenir la résistance mécanique attendue.
Le futur du déroulage
Il est généralement admis que la technique du déroulage est aujourd’hui à maturité technologique même si des progrès peuvent encore être accomplis. Les constructeurs de machines travaillent actuellement à minimiser la taille du noyau de déroulage en réduisant son diamètre de 8 cm à 2,5 cm. Ce qui met en lumière l’impératif pour notre industrie de maximiser l’emploi de la matière, plus précieuse que jamais.